Water Cooling : Coolant Compatibility and Electrolysis
After experiencing a few coolant incompatibilities and issues with corrosion, I performed these experiments with samples of all materials in the system. Tap water, distilled water, Water Wetter, and antifreeze solutions were tested.
Background and Objectives
Wanting to prevent corrosion, electrolysis, and any sort of biological growth, I initially used a solution of antifreeze and water as coolant. A short while later, I noticed that some of the nylon hose barbs I had used began to turn a bright green, as if they were absorbing the antifreeze. There were no indications of structural changes in the plastic, just the color, indicating some sort of reaction. The next time I drained the reservoir a few months later, a stringy white polymer had formed, floating on the surface of the water and being sucked against the grate of the pump inlet. I was quite sure beforehand that PVC and ethylene glycol were safe, but I had no real way of knowing the composition of the plastic reservoir, and the nylon fittings were clearly incompatible. Obtaining a new polyethylene reservoir and replacing all plastic fittings with brass has alleviated this issue, but has not addressed possible interactions of the various metals used.
Mixing different metals in a electrolytic solutions, such as water, has the potential of causing galvanic corrosion as one metal serves as an anode for the other. While the majority of my cooling system are either plastic or copper, some of the older waterblocks I am using are made of aluminum. As such, the corrosion properties of each have become of particularly keen interest to me. On more than one occasion, I have found the slower flowing, more restricted aluminum waterblocks to be clogged with light green precipitates, clearly the result of reaction with soluble copper ions and the aluminum metal. Short of replacing all aluminum components with a less corrosive material, I have investigated various solutions to minimize this issue of corrosion.
My particular problem has been most thoroughly studied with respect to automobile engines, often made of various aluminum and copper alloys. Typical resolutions involve sacrificial anodes such as magnesium, applying protective coatings to the easily corroded components, and addition of additives to the cooling system water to minimize its electrolytic properties. Antifreeze, largely composed of ethylene or propylene glycol, while serving a dual purpose of suppressing the freezing point of water, is sold to decrease corrosion. Redline's Water Wetter, a soluble oil, is sold to minimize corrosion and increase the heat transferring properties of water. In its essence, they seem to advertise that their product will reduce the amount of bubbles on hot surfaces, allowing for greater contact with the water. As I am not dealing with extreme temperatures or surfaces above boiling temperatures, I am interested solely in their anti-corrosion properties.
Similar Work
A common topic on the overclocking sites, I have been able to locate a number of references as to which coolants one should use. Unfortunately, the great majority of this information is anecdotal, unsupported by even the loosest of scientific reasoning, or is biased toward achieving the best 'performance', whatever that may infer. As I'm unlikely to blindly accept any so obtained data, I have sought to satisfy my own specific needs with appropriate tests.
Nonetheless, here are a few interesting links I have been able to locate:
Methods
As the objective was to qualitatively estimate the amount of corrosion in various coolant solutions, roughly equal samples of the various metals used in the system were combined in each of four solutions, covered, and let sit. The solutions were kept at room temperature with no agitation. They were analyzed visually, with scans taken at 11 and 23 days, shown below.
Materials
Sampled Material | Cooling Component |
Copper wire/pipe | Copper piping, waterblocks |
Steel window screen | Pump particle filter |
Galvanized Washer | Possible pump components, cases in event of leaks |
Aluminum foil | Used in place of actual aluminum. May not be representative. |
Brass screw | Various hose barbs, fittings |
Silver Solder | Unknown |
Solutions
- Tap water
- Distilled water
- Distilled water/Antifreeze
- Distilled water/Redline Water Wetter
Preliminary Results
While the experiment is still ongoing, the properties of each solution were readily evident within a matter of days. As can be seen in the photos below, both the distilled and tap water show significant corrosion of the galvanized washer as well as the immediately surrounding materials. While not adequately captured by the scanner, the distilled water solution contained a significant amount of suspended precipitates, especially at 23 days. Note that the distilled water aluminum foil sample happened to have a air bubble and floated, making it invisible in these scans. The Water Wetter solution showed corrosion only of the aluminum foil, something no other solution exhibited. I am not yet sure what to make of this. The antifreeze has showed no corrosion to date. Given the plastic incompatibilities described in the background section above, I'm still reluctant to go back to antifreeze and currently am running a dilute solution of Water Wetter while keeping an eye on the aluminum components. I have experienced no further oxide precipitates or noticeable corrosion thus far.
11-days
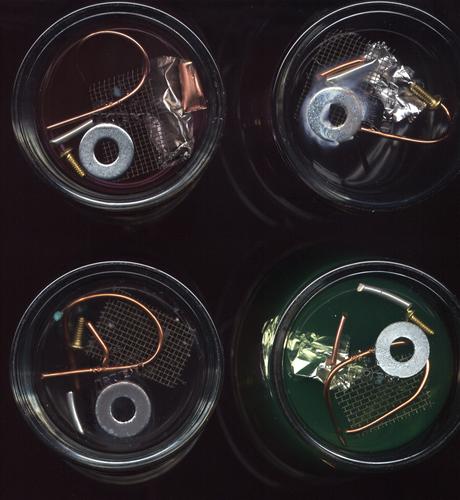
CW from top left: Water Wetter, tap Water, Antifreeze, distilled water.
23-days
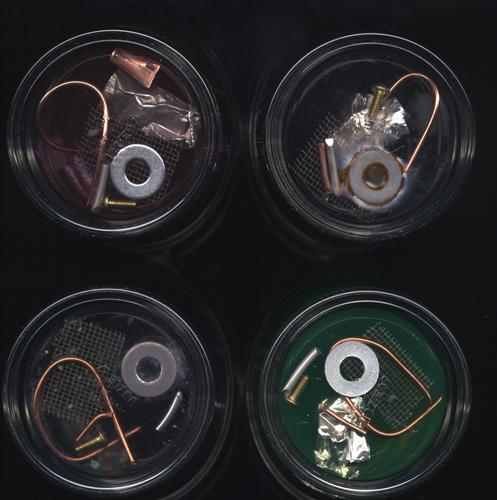
CW from top left: Water Wetter, tap water, Antifreeze, distilled water.
Last Modified: 17 Nov 2009